Polar Light and Finetech partner on next gen MicroLED tech
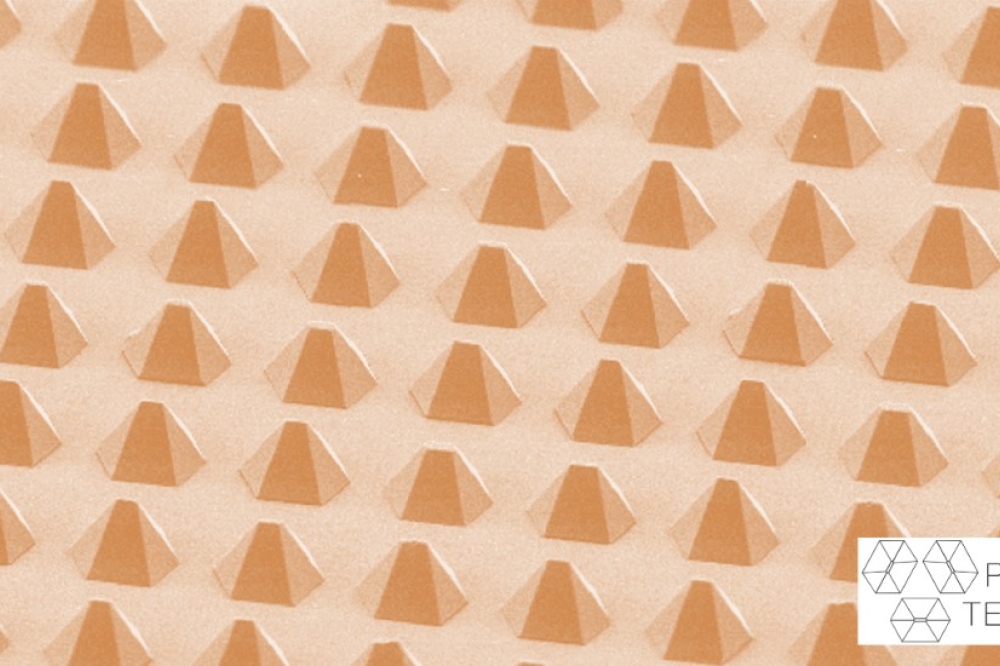
Swedish company Polar Light Technologies, a developer of microLED, has announced a partnership with German-based Finetech, a supplier for sub-micron and high-accuracy die bonding solutions.
The collaboration has already yielded significant advancements in micro-LED technologies for next generation AR, HUD and HMD applications.
Polar Light Technologies has a display technology that uses GaN pyramidal microLEDs directly bonded to Indium pads on a silicon chip. This new method, where LEDs are built from the bottom up, is designed to avoid the surface damage seen in traditional top-down methods, resulting in much better optical performance.
According to the company, the pyramidal shape of these LEDs allows for the creation of very small LEDs that are brighter and more efficient at emitting light by reducing energy losses and increasing their energy efficiency.
To connect these pyramidal microLEDs to silicon substrates, Polar Light Technologies teamed up with Finetech to develop a cold bonding technique that ensures accurate alignment with the electronics. In early trials, this method showed an 85 percent success rate, proving its potential for large-scale manufacturing.
Polar Light’s makes the display front panels using atomic layer regrowth of the GaN pyramids on a SiC substrate. This method produces microLEDs as small as 300 nm, without the damage caused by traditional top-down methods. As a result, the devices are said to have near-perfect surfaces, which is crucial for optical properties.
According to the company, these MicroLED displays can fit the resolution of a full TV screen into an area smaller than 5 mm², with about 1,000 by 1,000 connection points spaced just 5 µm apart. Polar Light’s design also significantly reduces energy use, making these microLEDs highly efficient for next-gen micro displays.
Compared to regular LEDs, the pyramidal microLEDs are claimed to improve AR system efficiency by 50 to 200 times thanks to better internal and external quantum efficiencies and enhanced light utilisation. By minimising internal electric field interference and optimising the interaction between charge carriers in the quantum wells, these microLEDs produce more light with sharper, more narrow emission. This makes them suitable for applications like augmented reality (AR) and micro-projectors, where precise light control is important.
A complete microLED display consists of three main parts: the front panel (the actual display), the back panel (which includes all the electronics), and the connection between the two. For the process of connecting the front panel to the back panel made of silicon, a modified flip-chip bonding method was used. In this process, the metallised GaN pyramids are precisely aligned and bonded to the Indium pads on the silicon back panel.
Because of differences in how SiCand silicon expand with heat, no heat could be used during the bonding process. Finetech and Polar Light Technologies developed a cold compression bonding method for aligning and bonding MicroLED arrays using an automated FINEPLACER femto 2 sub-micron die bonder. This machine ensures excellent process control, with high accuracy in flatness, alignment, and bonding force, which is crucial for connecting the fine-pitch Indium bumps for high-performance displays.
In addition to its precision, the FINEPLACER die bonder is said to be flexible enough to scale up production and adapt to new MicroLED technologies. Finetech also provides solutions for handling materials and cleaning with chemical or atmospheric plasma to avoid damage or contamination. This system allows for easy flipping of delicate Indium bump arrays without tweezers, and it ensures the materials are treated before bonding to improve overall quality.